Unleashing the Power of Tensile Fabric Structures
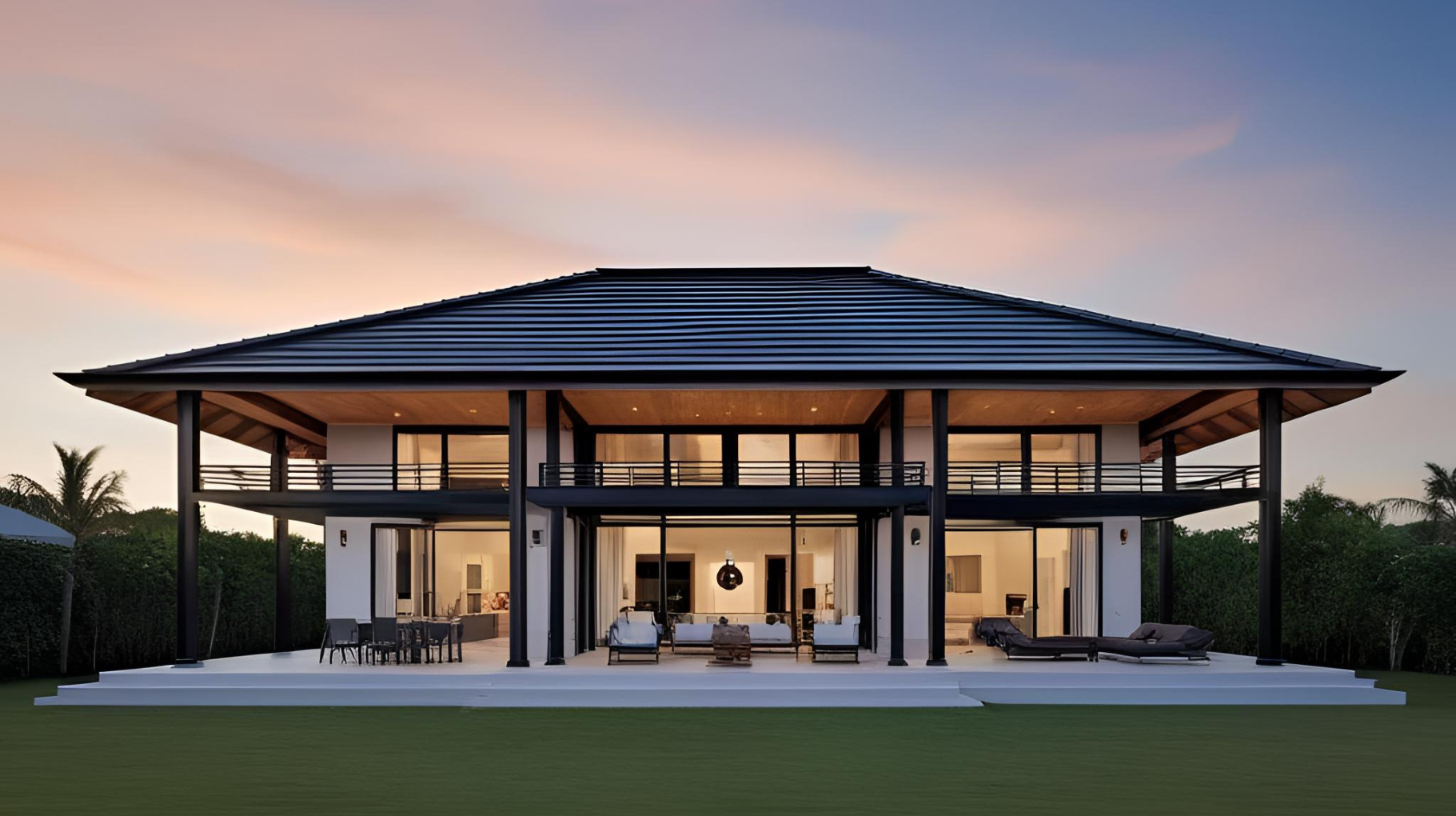
Tensile fabric steel structures are commonly used for sports stadiums, tennis courts, swimming pool enclosures, and gymnasiums. The fabric’s ability to span large distances without internal support columns makes it ideal for open, unobstructed spaces.
These structures are often used for temporary and permanent event venues, trade show pavilions, concert stages, and festival tents. They provide a sleek, modern look and can be quickly assembled and disassembled, making them perfect for large-scale events.
Tensile fabric canopies are often used for carports and parking structures. These provide cost-effective, weather-resistant solutions that protect vehicles from sun, rain, and snow while reducing the need for heavy, complex construction.
Large-scale warehouses, industrial storage, and manufacturing facilities can benefit from tensile fabric steel structures. The large spans provide unobstructed space for machinery, goods, and operations while keeping construction costs low.
In agriculture, tensile fabric steel structures are utilized for greenhouses, storage sheds, and livestock shelters. The lightweight yet strong fabric provides excellent light transmission, promoting healthy plant growth, while the steel frame offers stability and durability.
Tensile fabric structures are used for museums, community centers, and public gathering spaces. Their modern aesthetic and ability to create unique architectural shapes make them popular for iconic buildings in civic and cultural developments.
Glamping tents made of tensile fabric structures offer the perfect blend of durability, style, and comfort for luxury outdoor stays. The lightweight yet strong tensile fabric allows for striking designs that are weather-resistant, breathable, and adaptable to various climates. Supported by steel or aluminum frames, these structures create spacious interiors that can be customized with upscale amenities like plush beds, elegant lighting, and private bathrooms. Ideal for eco-resorts, campgrounds, and private retreats, tensile fabric glamping tents deliver a unique experience where guests can enjoy nature without compromising on comfort or luxury.
The first step in creating a tensile fabric structure is the design and engineering phase. Experienced architects and engineers work closely with clients to understand the project’s purpose, location, and environmental conditions. Using advanced 3D modeling software, they design the ideal shape, optimize tension distribution, and ensure the structure meets wind, snow, and load requirements. This careful planning ensures the final tensile fabric installation is not only visually stunning but also safe, durable, and efficient.
Choosing the right tensile fabric material is crucial for performance and longevity. Depending on the project needs, materials like PTFE-coated fiberglass, PVC-coated polyester, or ETFE membranes are selected for their exceptional durability, UV resistance, fire rating, and aesthetic appeal. Each material offers specific benefits, such as self-cleaning properties, light transmission, or flexibility, ensuring the structure performs optimally in its intended environment while maintaining a sleek and modern look.
Once the design and materials are finalized, the tensile fabric moves into the patterning and fabrication phase. Precision-cut patterns are created using CAD software, allowing the fabric panels to fit perfectly over the frame. Skilled technicians weld or sew the fabric panels using high-frequency welding or thermal bonding techniques to create strong, seamless membranes. This precise fabrication process ensures a flawless appearance and exceptional structural performance.
The supporting frame is a critical part of any tensile fabric structure. Steel or aluminum components are custom-fabricated to match the unique design and calculated tension loads. The frame provides the necessary strength to support the fabric membrane while withstanding environmental pressures. Every beam, mast, and connection point is engineered for safety, durability, and easy assembly, ensuring a reliable framework for the fabric installation.
Before installation, the project site is carefully prepared to accommodate the tensile fabric structure. This includes setting foundations, anchor points, and drainage systems as required by the design. Concrete footings or embedded steel plates are installed to secure the frame and membrane safely. Proper site preparation ensures a smooth installation process and provides the foundation for long-term structural stability.
Installation is where the tensile fabric structure comes to life. The steel or aluminum frame is assembled on-site, followed by lifting the pre-fabricated membrane panels into place using cranes or specialized equipment. The fabric is attached to the frame with tensioning hardware, carefully stretched to achieve the desired shape, tension, and performance. Proper tensioning is critical to ensure weather resistance, longevity, and the signature sweeping forms that tensile structures are known for.
X3 Capsule House
Shark Cabin
G9 SPACE CAPSULE
G8 SPACE CAPSULE
G6 SPACE CAPSULE
A tensile fabric structure is an architectural system that uses tensioned fabric membranes, supported by steel or aluminum frames, to create lightweight, durable, and visually striking buildings or canopies.
With proper maintenance, tensile fabric structures can last 20–30 years or more, depending on the material and environmental conditions.
Key benefits include lightweight construction, rapid installation, flexible design options, energy efficiency, durability, and eye-catching aesthetics.
Depending on the size and complexity, installation can take from a few days to several weeks, significantly faster than conventional construction.
High-quality membranes meet international fire safety standards and have excellent fire-resistant or fire-retardant properties
Common materials include PTFE-coated fiberglass, PVC-coated polyester, and ETFE film, each selected for strength, flexibility, UV resistance, and durability.
Yes, most tensile membranes are fully waterproof, providing excellent protection from rain, snow, and harsh weather.
They are installed by assembling the supporting steel or aluminum frame on-site, lifting the fabric membrane into place, and tensioning it securely.
Minimal maintenance is needed—typically routine inspections, cleaning, and occasional tension adjustments to maintain performance.
Yes, most designs require foundations, which may include concrete footings or embedded steel plates, to anchor the frame securely.